Nachrichten & Pressemitteilungen
Wo rohe Kräfte sinnvoll walten
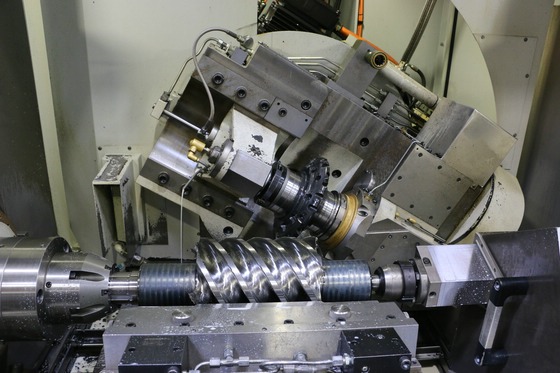
FRÄSEN – Soll das Bauteil senkrecht oder besser waagerecht aufgespannt und bearbeitet werden? Die höhere Stabilität und die gesamte Prozesskette sprachen bei der GEA Refrigeration Germany in Berlin für die Horizontalbearbeitung. Mit einer Profilfräsmaschine der Serie Holroyd EX lieferte PTG dafür die passende Lösung.
Zu DDR-Zeiten hat der VEB Kühlautomat in Ostberlin eine Zeit lang auch ganz normale Kühlschränke produziert. Immer mehr kristallisierten sich dann große Kühlanlagen als Hauptgeschäftsfeld heraus. Sie gingen etwa an die Werften in Rostock und Stralsund und wurden in große Fischtrawler eingebaut, die ihren Fang gleich an Bord verarbeiteten und beispielsweise als tiefgefrorene Fischstäbchen in die Häfen brachten. Zu Spitzenzeiten arbeiteten beim VEB in Berlin-Johannisthal 2.000 Mitarbeiter in einem 190.000 Quadratmeter großen Werk auf dem Gelände des alten Flugplatzes im Südosten Berlins.
1994 ging die Firma an den GEA-Konzern und zog 1996 nach Berlin-Reinickendorf um. Die hier produzierten Industriekälteanlagen dienen dem Kunden zu ganz unterschiedlichen Zwecken. Kältetechnik ist ein unabdingbarer Bestandteil für die Nahrungs- und Genussmittelindustrie. Daher liefert die GEA in allen Phasen des Wertschöpfungsprozesses, von Produktion über Transport bis zur Bereitstellung verderblicher Güter, Komponenten für Lebensmittelunternehmen und Brauereien. Weitere große Einsatzgebiete sind die Gebäudeklimatisierungen für Bürokomplexe, Messe-, Industrie- und Produktionshallen sowie Testcenter für Fahrzeuge und Motoren. Aber auch die Nachfrage im Sportbereich, wie zum Beispiel von Eis- und Skihallen (Olympische Spiele London, Skihalle Dubai), Bobbahnen oder Kreuzfahrt-
schiffen, wächst stetig. „Wir sind überall da, wo Kälte in großen Mengen gebraucht wird“, fasst Produktionsleiter Hanno Heim das vielseitige Geschäft zusammen.
Das Werk in Berlin hat sich auf Kühlaggregate und Flüssigkeitskühlsätze mit Schraubenkompressoren spezialisiert. Mit der Grasso M und den größeren Grasso LT werden zwei unterschiedliche Schraubenverdichterserien angeboten. Verschiedene Untergruppierungen lassen daraus 24 Grundtypen des Schrauben-
verdichters in unterschiedlichen Größenordnungen entstehen. Von kleinen Kompressoren mit 231 Kubikmetern Volumenstrom bis zum 11.500-Kubikmeter-Aggregat reicht das Spektrum.
Wie jeder Kühlschrank besteht auch eine Industriekälteanlage aus Kompressor, Verflüssiger, Expansionsventil und Verdampfer, nur ist hier alles etwas größer. Herzstück eines jeden Kompressors ist der Rotor, beziehungsweise sind die Rotoren, denn verbaut werden jeweils ein Haupt- und ein Nebenrotor. Aufgrund
der modernen Fertigung können im Gegensatz zu früher unterschiedliche Unter-
gruppierungen der Rotoren miteinander kombiniert werden. Dabei haben Pass-
genauigkeit und die Einhaltung der Toleranzen höchste Priorität. Der Hauptrotor wird, um die Kompression in Gang zu setzen, durch einen Elektromotor über eine Kupplung angetrieben, dessen Antriebsleistung von 75 Kilowatt bis an die 5 Megawatt reicht.
Maschinen-Mix
Während die Bearbeitung der Gehäuse mittlerweile ausschließlich auf Starrag-Heckert-Maschinen erfolgt, findet sich in der Fertigung der Kompressorschrauben ein recht gemischter Maschinenpark. Die Herstellung der Rotoren erfordert einen komplexen technologischen Durchlauf. „Um den Rotor fertigzustellen, haben wir neun verschiedene Fertigungsprozesse, die jeder Rotor durchlaufen muss“, berichtet Markus Schiemann, Prozessingenieur bei GEA.
Für die meisten Rotoren kauft GEA die Rohlinge als Stangenmaterial ein, welches auf einer Drehmaschine vorbearbeitet wird, so dass zuerst die groben Außenkonturen entstehen. Für die größeren Typen wird geschmiedetes Material, welches bereits vorgedreht und geglüht ist, verwendet. In beiden Fällen besteht das Material aus C45N, also klassischer Maschinenbaustahl. Die kleineren Rotoren werden an-
schließend in einen Glühofen gepackt und bei 580 Grad spannungsarm geglüht. Schwarz kommen sie zur weiteren Bearbeitung in die Halle zurück. Hier erfolgt anschließend auf einer zweiten Drehmaschine die Finish-Bearbeitung, bei der die Bauteile auf das Schleifmaß gebracht werden. In diesem Schritt werden auch sämtliche axiale Bohrungen eingebracht, Gewinde geschnitten, Einstiche gesetzt und Nuten gefräst. Für viele Rotoren ist das Laserhärten der Lagerstellen durch einen Roboter der nächste Bearbeitungsschritt.
Noch sind die Rotoren einfache runde Wellen mit verschiedenen Durchmessern. Ihre charakteristische Form bekommen Haupt- und Nebenrotor beim Vor-
profilieren, wo das schraubenförmige Profil herausgefräst wird. Dieser entscheidende Arbeitsschritt war lange Zeit das Sorgenkind der Fertigung. Über die Jahre wurden dafür verschiedene Maschinen eingesetzt, die zumeist noch aus DDR-Zeiten stammten. Bis vor einiger Zeit wurden noch 30 Jahre alte Modul-Maschinen zum Vorfräsen des Profils im Einzelteilfräsverfahren eingesetzt. Trotz Retrofits an den Maschinen waren die Bearbeitungszeiten zu lang und die größten Rotoren konnten nur mit mehrmaligen Umspannen bearbeitet werden. Daher war eine Neuinvestition dringend notwendig, um nach dem Stand der Technik fertigen zu können.
Einen Makel hatte das seitherige Vorprofilieren von Haus aus: Auf den vorhandenen Maschinen konnte dieser Bearbeitungsschritt nur vertikal erfolgen. Im Prinzip wurde hier eine Zahnradfräsmaschine zweckentfremdet, deren Planscheibe mit 1,20 Meter Durchmesser eigentlich dazu gedacht war, bis zu zwei Meter große Zahnräder zu bearbeiten. Um darauf einen Rotor zu bearbeiten, musste man mit einem Sonderfräskopf nah an das Bauteil heranfahren. Da das Bauteil in der Mitte der Planscheibe gespannt wurde, war es zum Teil schwierig den Rotor zu erreichen. Die Bearbeitungssituation war eher labil.
Immer Vibrationen
Hanno Heim geht ins Detail: „Die Maschinen hatten einen großen Fahrständer mit einem Fräskopf und einen Gegenständer zur Halterung der Rotoren. Auf dem Maschinentisch befand sich die große Planscheibe, auf der wiederum die Vorrichtung aufgebaut wurde. Um den Rotor richtig spannen zu können, wurde dieser mit einer Spitze gehaltert. Dermaßen aufgespannt, war der Rotor praktisch frei schwebend und somit waren Vibrationen unvermeidlich.“
Mit dem Austausch der alten Maschinen wollte GEA auch technologisch einen Sprung nach vorn machen. Dabei hatten die Verantwortlichen in Berlin von Anfang an Holroyd auf ihrer Liste. Maschinen des englischen Herstellers waren hier bereits zu DDR-Zeiten noch vor den Modul-Maschinen im Einsatz und sind bis heute bei manchem Werker in guter Erinnerung geblieben. Vor dem Kauf wurden allerdings auch mögliche Alternativen überprüft. Wiederum hätte in allen Fällen weiterhin vertikal gefräst werden müssen – also genau das, was GEA nicht mehr wollte.
Besser horizontal
Johann Haugg, Deutschland-Geschäftsführer bei Holroyds Mutterkonzern PTG (Precision Technologies Group) weiß um das Alleinstellungsmerkmal seiner Maschinen: „Rotoren sind von Haus aus immer wellenförmige Teile und da eignet sich die horizontale Bearbeitung besser. Darum sind auch die Nachfolgemaschinen für Bearbeitung wellenförmiger Teile immer als Horizontalmaschinen ausgeführt. Beim Zahnrad überwiegt das scheibenförmige Stirnrad, das genauso horizontal bearbeitet werden könnte. Irgendwann um 1900 hatte sich die vertikale Bearbeitung eingebürgert. Über viele Jahrzehnte wurden auch in der Zahnrad-
produktion für die Fertigung so genannter Ritzelwellen auch horizontale Maschinen genutzt, die wurden dann aber größtenteils wieder eingestellt. Heute werden sie nur noch für kleine Teile bis Modul 2 eingesetzt, wo diese Vorteile genutzt werden. Ansonsten hat sich aber die vertikale Bauweise etabliert.“
In der GEA-Fertigung ist zu sehen, dass nicht nur die Nachfolgemaschinen in der Bearbeitungskette horizontal sind, sondern auch die vorbereitenden Arbeiten, ehe es ans Vorprofilieren geht. Für diesen einzelnen Schritt war also zweimaliges Umrüsten mit Hilfe von Transportgestellen erforderlich – ein vor allem bei großen Rotoren mühsames Handling.
Fräser gehen zur Sache
Dieses Problem ist nun seit gut einem Jahr mit der Inbetriebnahme der Holroyd 4EX-R-XL Rotorfräsmaschine gelöst. Auf ihr können sämtliche Rotorvarianten der GEA horizontal bearbeitet werden. Die kleinsten Hauptrotoren sind 320 Millimeter lang und haben einen Durchmesser von 120 Millimeter, die größten messen dagegen zwei Meter mit einem Durchmesser von 430 Millimeter. Das Gewicht eines Teils liegt dabei zwischen knapp 10 Kilogramm und einer Tonne. Die Dimension der Maschine wurde so gewählt, dass sie sich sowohl für kleinere als auch für die ganz großen Bauteile eignet. Die Frässpindel mit einer Leistung von 63 kW verleiht der Maschine auch genug Kraft, um die nun wesentlich stabilere Aufspannsituation zu nutzen. „Mit unseren Scheibenfräsern gehen wir beim Profilieren auf Schnitttiefen bis 40 Millimeter und fahren mit Schnittgeschwindigkeiten von bis zu 300 Millimeter pro Minute“, berichtet Prozessingenieur Markus Schiemann. Auf den alten Vertikalfräsmaschinen waren solche Werte undenkbar.
„Die Holroyd ist eine Rotorfräsmaschine, die speziell für das Fräsen von Rotoren konzipiert wurde und nicht für größere Zahnräder“, erklärt Hanno Heim. Johann Haugg ergänzt: „Wer großmodulige Zahnräder herstellt, hat in Relation nicht dieses hohe Zerspanvolumen wie bei Rotoren. Holroyd baut seit jeher horizontale Maschinen für schneckenförmige Drehteile. Grundthematik ist dabei ein steifes Maschinenbett, um die auftretenden Kräfte abzuleiten.“
Von den Kräften, die am Werke sind, ist vor der Maschine kaum etwas zu spüren. Der Prozess läuft sehr ruhig ab. Hier zeigt sich der große Vorteil dieses Bearbeitungsverfahrens: Die Schnittkraft wird über Bauteil und Schrägbett ins Fundament abgeleitet. Weil die Kraft dabei auf einer Linie wirkt, treten so gut wie keine Schwingungen auf. Die Holroyd wartet mit noch einer Besonderheit auf: Während die Vorgängermaschinen immer nur eine Nut nach der anderen bearbeiten konnten, fräst die Holroyd stets die gegenüberliegende Nut als nächste. Energie- und Krafteintrag bleiben so weitgehend konstant.
Kraft wird abgeleitet
Die Kräfte gelangen über eine relativ einfache, robuste Vorrichtung auf die Maschine. Bei kleineren Rotoren geben zwei massive Stützplatten ausreichend Halt, für größere werden zusätzlich noch zwei Lünetten eingesetzt. Die Vorrichtung erlaubt nicht nur vibrationsfreies Fräsen, sondern führt auch Wärme ab.
Unterstützend wird während der Bearbeitung das Bauteil gekühlt, obwohl es sich grundsätzlich um eine Trockenbearbeitung handelt. Während es früher Wärme-
einträge bis zu 150 °C gab, kommen die Teile nun handwarm von der Maschine. Das kommt der Genauigkeit und der Werkzeugstandzeit zugute. „Wir sind nun in der Lage, die doppelte Losgröße fertigen zu können, ohne die Wendeschneidplatten wechseln zu müssen“, freut sich Hanno Heim.
Eine Maschine weniger
Vor allem aber spart GEA mit der neuen Holroyd 4EX, die seit ihrer Inbetriebnahme in mindestens zwei Schichten läuft, viel Zeit. Das Vorprofilieren auf der Holroyd dauert je nach Dimension des Rotors 10 bis 100 Minuten. Früher lagen die Zeiten zwischen 25 Minuten und vier Stunden. „Wir können das, was zuvor auf zwei Maschinen produziert wurde, nun auf einer einzigen fertigen“, berichtet Hanno Heim. „Wir haben die Bearbeitungszeiten um 40 bis 60 Prozent gesenkt. So konnten wir mit einer neuen Maschine zwei alte ausmustern, genau das war auch unser Ziel.“
Platz sparen ist ein großes Thema bei GEA. Nach dem Umzug im Jahr 1996, an den Standort in Berlin-Reinickendorf, standen dem Unternehmen anstelle eines großen Geländes auf einem alten Flugplatz nur noch 27.000 Quadratmeter zur Verfügung. Ausgelegt war das Werk ursprünglich für die Fertigung von jährlich 600 Schrauben-
verdichtern und 150 Verdichteraggregaten. Heute werden auf der gleichen Fläche rund 1.500 Schraubenverdichter und 400 Aggregate produziert. Und die Stück-
zahlen steigen weiter. „Man kann sich vorstellen, dass dies nur durch intensive Rationalisierungen möglich ist“, so der Produktionsleiter. „Darauf achten wir ganz besonders, wenn Maschinen und Anlagen erneuert werden.“
Abläufe optimiert
Die Holroyd 4EX fand Platz auf dem Fundament einer der beiden Vorgänger-
maschinen. Der zweite frei gewordene Platz wurde dazu genutzt, Prozessabläufe zu optimieren. Der Maschinenbediener findet nun Werkzeuge sowie Vorrichtungen in seiner unmittelbaren Umgebung vor, wodurch sich seine Laufwege deutlich reduziert haben. Stück für Stück konnten so Rüstzeiten verkürzt werden.
Zu den schnelleren Bearbeitungszeiten tragen auch neue Werkzeuge für die unterschiedlichen Rotoren bei, die sich GEA im Zuge der Maschineninvestition zugelegt hat. Mit dem langjährigen Werkzeugpartner Kennametal haben die Berliner hier gute Erfahrungen gemacht. Das Zusammenspiel zwischen Maschine und Werkzeugen erhöht schon beim Vorfräsen die Genauigkeit, was bei den abschließenden Finish-Bearbeitungen wiederum Bearbeitungszeit spart und dafür sorgt, dass die eingesetzten Finish-Werkzeuge länger halten. Grund dafür ist die deutlich genauere erzeugte Profilkontur im Vorfräsprozess.
Das Ziel, die Fertigungsprozesse und Arbeitsabläufe in der Fertigung der Rotoren bei der GEA zu modernisieren und zu optimieren, dabei auch die Durchlaufzeiten der Rotoren zu kürzen, ist mit der Investition der Holroyd 4EX gelungen.