News & Press
More Than £4 Million in Orders from Global Air Compressor Sector for Holroyd Precision
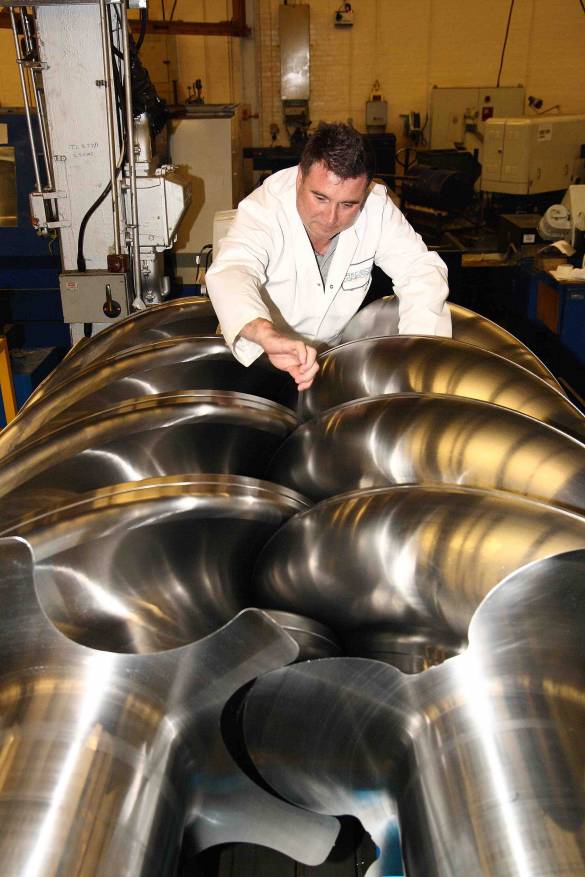
Valued at £3.3 million, the order from China is for a Holroyd 8EX rotor milling machine that is capable of milling profiles of up to 850mm in diameter, and a Holroyd TG350E (350mm diameter capability) rotor grinding machine.
‘Next generation’ technologies
Valued at £3.3 million, the order from China is for a Holroyd 8EX rotor milling machine that is capable of milling profiles of up to 850mm in diameter, and a Holroyd TG350E (350mm diameter capability) rotor grinding machine. Offering ‘next generation’ production technologies, both models are renowned across industry for their high stock removal rates and high levels of accuracy. The customer concerned is a manufacturer of specialist oil-free air compressors that are used in the medical and textile sectors. The TG350E rotor grinding machine will be shipped in December 2013; the 8EX rotor milling machine will follow in early 2014.
The order from Germany is for a Holroyd 3EX-R rotor milling machine. Valued at £1 million, it has a 350mm maximum diameter capability and will be used by a premier air compressor manufacturer for the milling of screw profiles.
Full design, software and support
With unparalleled technical knowledge and expertise in milling and grinding profiles, Holroyd Precision Ltd. is able to offer a range of services that extends far beyond the design and build of machine tools that are tailored to each customer’s precise requirements. In the case of the order from China, Holroyd will also provide compressor designs and the latest high-efficiency rotor profiles.
Support from City University, London
To assist the Chinese customer in ongoing profile and compressor development, it has also been arranged for their profile development team to attend City University, London, Holroyd Precision’s technology partner in compressor development, for tutoring in compressor design.
HPMS – advanced profile management
As an additional customer benefit, the TG350E rotor grinding machine will be supplied with the Holroyd Profile Management System (HPMS) – a desktop profile manufacturing and design tool that is recognised globally as providing unrivalled profile, clearance and tool development capabilities.
Leading-edge milling and grinding
“We are delighted to have been asked to supply our leading-edge milling and grinding technologies to the organisations concerned,” comments Holroyd Precision’s Sales Manager, Steven Benn. “Holroyd EX and TG models are renowned for their capabilities across applications as wide ranging as air conditioning, superchargers, gas screw compressors and hydraulic pumps.”
PTG. The first name in precision
Incorporating the brands of Holroyd, Binns & Berry, Crawford Swift and Precision Components, PTG has established itself at the forefront of high precision machine tool design, build and supply. The PTG range includes ultra precision grinding machines for rotor, thread and gear operations; rotor milling machines; heavy duty lathes; deep hole boring machines; friction stir welding machines and special purpose machine tools for the manufacture of precision components. Industrial sectors served range from aerospace, medical and mould tool & die to marine, power generation, mining, oil & gas, steel, high end and heavy automotive.
Photograph caption:
Absolute precision in rotor milling: large diameter rotors, milled using a Holroyd 8EX machine.
For more press information, please contact:
Neil Jones – Group Business Development Director, PTG
Tel: +44 (0) 1706 526 590
Email: neil.jones@ptgltd.com